在矿山、冶金、水泥等行业中,槽帮(如输送槽、溜槽等)长期承受物料冲击与磨损,易出现局部变形或磨损穿孔。采用堆焊焊丝进行修复,既能恢复结构强度,又能提升表面耐磨性。然而,焊接过程中若操作不当,易出现裂纹、气孔、夹渣等缺陷,直接影响修复效果与设备寿命。本文从堆焊焊丝的优势出发,结合常见缺陷成因,提供系统性解决方案。
一、堆焊焊丝修复槽帮的独特优势
1、高效修复与耐磨强化
堆焊焊丝通过熔敷高硬度合金层(如碳化铬、碳化钨等),可快速填补槽帮磨损区域,同时形成耐磨保护层,减少后续磨损速率。
2、灵活适应复杂工况
根据物料特性(如硬度、腐蚀性),可选择不同成分的焊丝(如高铬铸铁系、镍基合金系),针对性应对冲击、腐蚀或高温环境。
3、经济性与环保性
相比更换新部件,堆焊修复可节约70%以上成本,且减少资源浪费,符合可持续发展理念。
二、槽帮堆焊修复中的常见缺陷及成因
1、裂纹
冷裂纹:焊后冷却过快或焊丝含氢量高,导致焊缝金属脆化;
热裂纹:焊接过程中热应力集中或材料成分偏析(如硫、磷杂质)。
2、气孔与夹渣
焊前清理不彻底(油污、锈迹)、焊丝受潮或保护气体不足;
焊接电流不稳定或焊速过快,熔池凝固时气体未及时逸出。
3、未熔合与咬边
焊枪角度不当或焊接参数(电流、电压)不匹配,导致母材与焊层未充分结合;
焊道重叠区域处理不当,边缘形成凹陷。
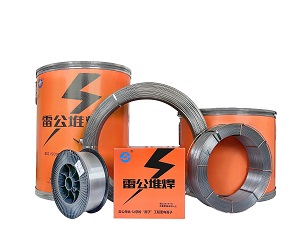
三、避免焊接缺陷的关键措施
1. 焊前准备:奠定高质量修复基础
彻底清洁槽帮表面:使用砂轮、钢丝刷清除油污、氧化皮及锈迹,避免杂质混入熔池;
预热控制:对厚壁或高碳钢槽帮进行预热,减少温差应力,防止冷裂纹;
焊丝干燥处理:受潮焊丝需在烘干箱中(300℃/1~2小时)除湿,降低气孔风险。
2. 优化焊接工艺参数
匹配电流与焊速:小电流适合薄壁槽帮修复,减少热输入;厚壁部位可适当提高电流,确保熔深;
多层多道堆焊:每层厚度控制在3mm以内,层间温度≤150℃,避免热积累导致变形;
合理选择保护气体:CO₂或混合气体(如Ar+CO₂)可稳定电弧,减少飞溅与氧化。
3. 操作技巧与过程控制
焊枪角度与运条方式:保持焊枪与工件70°~80°倾角,采用锯齿形或月牙形运条,确保熔合均匀;
控制焊道顺序:从槽帮边缘向中心焊接,减少收缩应力;对称焊接可平衡热变形;
实时监测熔池状态:观察熔池颜色与流动性,及时调整参数,避免夹渣或未熔合。
4. 焊后处理与检测
缓冷措施:焊后用石棉毡覆盖焊缝,自然冷却至室温,防止急冷开裂;
表面打磨与探伤:去除焊渣后,进行渗透检测(PT)或超声波检测(UT),确认无隐藏缺陷;
局部补焊优化:对检测出的微小气孔或裂纹,采用小电流补焊修复。
四、堆焊焊丝应用中的维护建议
1、定期巡检与预防性修复
在槽帮轻微磨损阶段及时堆焊,避免基材大面积损伤,降低修复难度。
2、焊丝选型与工况匹配
高冲击工况选择韧性好的马氏体钢焊丝;
高温腐蚀环境选用高镍合金焊丝。
3、建立标准化操作流程
制定焊接工艺卡,明确参数范围与操作规范,减少人为失误。
五、结语
堆焊焊丝修复槽帮是一项技术性与经验性并重的工作。通过精准选材、规范操作、焊后检测及预防性维护,可显著降低焊接缺陷风险,充分发挥堆焊层耐磨、抗冲击的优势。企业需结合设备实际工况,完善技术培训与质量管理体系,确保每一次修复都能延长槽帮寿命,为连续生产保驾护航。
以上内容由堆焊焊丝厂家天津雷公焊接材料有限公司编辑 咨询电话:18202593233